[box type=”note”]우리 주변의 전자제품이 탄생하는 한 예로써 ‘스위처’(핸드폰 앱으로 조작하는 무선 조명 스위치의 상품명)라는 제품이 만들어지는 과정을 공유합니다. 이 글은 스위처 제작사인 하드웨어 스타트업 ‘I/O’에서 작성했습니다. (필자) [/box]
일반적으로 제품이 만들어지고 시장에서 판매되기까지의 과정을 크게 나누면 개발 → 생산 → 유통이라 할 수 있고 우리가 여기서 스위처를 가지고 이야기하고자 하는 단계는 개발부터 생산까지다. 스위처의 첫 시작부터 생산까지의 일정은 아래와 같았다.
7개월이 걸렸다.
7개월 동안 1,700개. 어떤가? 7개월에 1,700개를 만들어 낸 일이 특별하게 느껴지지 않는 분들과 특별하게 느껴지는 분들 모두에게 우리 이야기를 들려주려 한다.
- 2015.2: 스위처 개발 시작
- 2015.4~5: 베타테스트
- 2015.6: 크라우드 펀딩 시작 및 성공
- 2015.9: 스위처 1,700대 생산완료
- 2015.2: 스위처 개발 시작
[divide style=”2″]
2015.2: 스위처 개발 시작
불 끄러 가기 귀찮다는 친구의 불평 한마디에 시작된 스위처 Small Project는 2월부터 상용 제품으로 개발이 시작됐다.
[divide style=”2″]
2015.4~5: 베타테스트
벽돌을 쥐는 느낌의 질감과 디자인을 무시 해버리는 색깔이었지만, 불을 켜고 끄는 기능은 문제없던 베타테스트 제품 30개를 3D 프린터로 제작했다. 우리는 이 30개의 스위처를 가지고 서울 전역 30명의 베타테스터들을 직접 방문하여 스위처를 소개하고, 2주간 서울 전역에 뿌려진 스위처를 통해 제품의 기능 문제와 사용자 관점에서 스위처가 가져가야 할 핵심가치를 발견하였다.
이 과정을 통해 제품 생산에 있어 생산속도 및 외형 품질 면에서는 3D 프린터가 아직은 대안이 될 수 없음을 알게 되었지만, 하드웨어를 테스트할 수 있는 최적의 도구임을 확인하였다. 특성을 잘 활용한다면 하드웨어 제조에 있어 3D 프린터의 활용가치는 무궁무진하다.
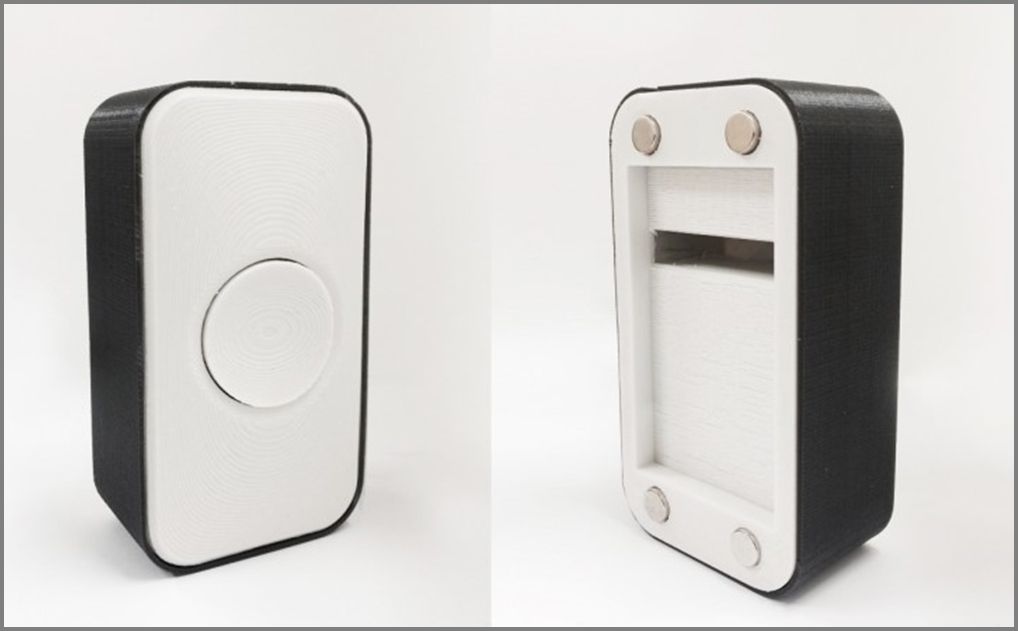
[divide style=”2″]
2015.6: 크라우드 펀딩 시작 및 성공
약 두 달에 걸친 베타테스트를 통해 사용자들이 쉽고 편리하게 쓸 수 있는 제품을 만들 수 있는 발판을 마련했고 우리는 스위처의 첫 시장 진출로써 크라우드펀딩을 선택했다.
여러 후원자의 응원과 관심 속에 모금률 100%(3,000만원 목표, 3,002만 5,000원 모금 ) 를 넘길 수 있었고 모금된 금액으로 스위처를 생산할 단계로 접어들 수 있었다.
[divide style=”2″]
2015.9: 스위처 1,700대 생산완료
[divide style=”2″]
왜 1,700개를 만드는 데 3개월이나 걸린 걸까?
크라우드펀딩에 참여하신 분들은 많이 궁금해하실 수 있는 부분이다. 크라우드펀딩에 성공하고 제품이 배송되기까지인 2015년 6월 ~ 2015월 9월 사이에 I/O는 어떤 일을 했을까? 그렇게 많게 느껴지지도 않는 1,700개를 생산하는 데 3개월이나 걸렸을까?
글을 쓰고 있는 나는 만들기를 좋아하는 사람이다. 스위처를 만들고 있는 지금도 스위처가 아닌 다른 무언가 만들어내는 것이 여전히 좋다. (가끔 근질근질해서 자잘한 것들을 만들기도 한다.)
재미난 물건들을 만드는 커뮤니티에 참가하고, 그것들을 공유하고 전시하는 행사에 참여하기도 한다.
하지만 이런 것들을 내 손으로 만들어내는 것들과 달리 상용제품을 개발해 수천 개 찍어내는 일은 단순히 1개 2개를 만들어내던 방법과 과정 그리고 비용이 아예 다르다.
- 나의 불편함을 해결하기 위해 A라는 물건을 1개 만들어 보았다.
- 물건이 썩 쓸만하니 주위에서 자기에게 팔라고 가만 놔두질 않는다.
- 솔깃한다.
- 한 1,700개를 만들어서 팔아볼까 다짐한다.
이런 상황에서 A를 만들 비용과 방법을 1,700번 반복하면 처음 만들었던 하나짜리 제품과 똑같은 1,700개를 만들 수 있을까? 만들 수 있을지도 모른다. 하지만 스위처가 그렇게 만들어지지는 않더라.
스위처의 생산 수량은 상승곡선을 그리며 단계를 거쳤고 각 단계마다 많아지는 수량에 따른 생산 전략이 필요했다.
스위처의 생산 수량을 시간 순으로 나열해보면
그리고 각 과정에서 제품을 생산하기 위해 중점적으로 사용했던 제품 생산 프로세스 4가지 단계는 아래와 같다.
- 커터칼 + 손
- 낡은 3D 프린터 + 여러 손
- 조금 쓸만한 3D 프린터 + 여러 손
- 사출 금형
- 커터칼 + 손 → 항상 해왔던 것이었고
- 낡은 3D 프린터 + 여러 손 → 내 손을 기계로 대체할 수 있음을 깨달았고
- 조금 쓸만한 3D 프린터 + 여러 손 → 그 기계를 잘 활용하는 법을 알게 되었으며
- 사출 금형 → 신세계를 맛보았다.
하드웨어 제품은 크게 외관과 내관으로 나눌 수 있다. 외관이란 직접 사람에게 보이는 부분이고 내관은 사람에게 보이지 않는 내부를 말한다.
외관은 디자인과 같은 미적인 요소와 많이 연관되고, 내관은 제품의 기본 기능을 위해 여러 구조물로 이루어진다. 다시 말해 외관이 안 예쁘면 사람이 눈여겨보지 않고, 내관에 문제가 있으면 제품은 동작하지 않는다.
두 요소 때문에 제품의 겉모양은 다양한 요구사항에 따라 자주 변경되기 좋다. 그 말은 제품의 설계 도면이 계속 바뀔 수 있다는 이야기이다.
하지만 이렇게 설계 도면이 계속해서 바뀌게 되면 본격적인 생산은 점점 뒤로 밀리게 되고 시기를 지난 제품은 고객에게 외면당하기 딱 좋다. 즉, 하루빨리 내·외관 모두 만족할 수준으로 확정 짓고, 그것을 ‘복사 + 붙여넣기’ 해서 고객들이 몰려드는 타이밍에 늦지 않게 시장에 내놓아야 팔리는데 설계를 확정 짓기가 여간 쉽지가 않다.
이는 똑같은 모습의 10,000개를 만들기가 쉽지 않을뿐더러 자칫 오류가 있는 제품을 섣불리 10,000개 만들었다가 전량 분리수거 해야 할 수도 있다는 두려움 때문이다. (다행히 플라스틱이면 재활용은 된다.)
그래서 I/O는 제품을 설계하고 개발하는데 QDO에 더욱 집중했다.
“Quick and Dirty One”
예쁘진 않지만, 핵심가치는 지니고 있는 제품으로 꾸준히 개선해 나간다. I/O의 업무 철학이다. 제품을 디자인하고 설계하는 데 있어서 영향을 줄 수 있는 분야를 크게 나누고, 하나하나씩 빠르게 검증해나가며 하나의 제품으로 합쳐나갔다.
소프트웨어에는 디버깅이라는 용어가 있다. 소프트웨어도 마찬가지로 처음 뚝딱 출시한 프로그램이 아무 오류 없이 동작할 일은 거의 없다.
다소 간단한 모바일 애플리케이션이라고 해도 다양한 부류의 사용자와 다양한 사용패턴으로 인한 예상치 못한 오류가 발생하는 경우가 많다. 그래서 디버깅이라는 과정을 거치면서 프로그램의 내부구조를 차근차근 훑어가며 오류를 생기게 한 요소를 없애나간다.
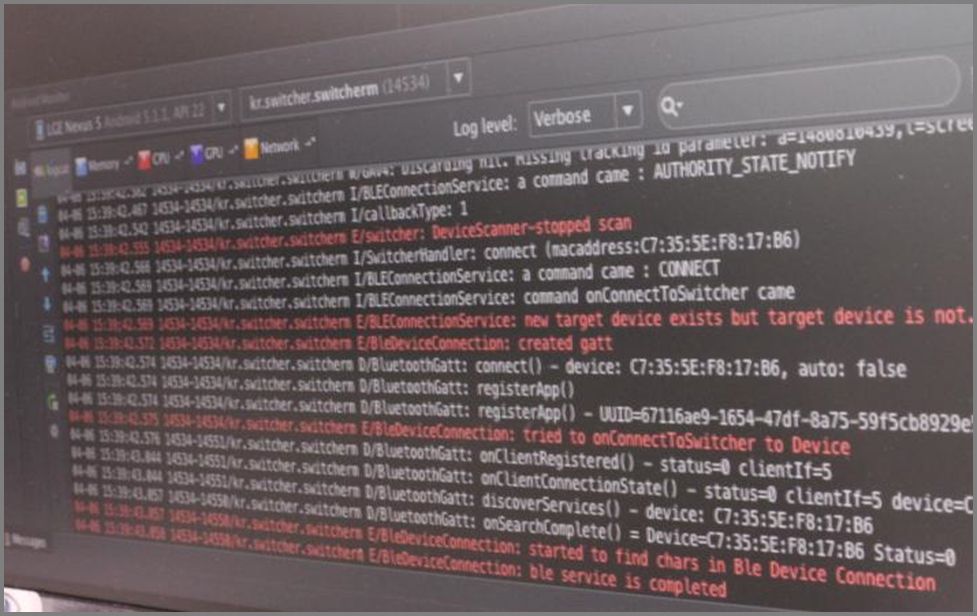
그리고 대개 이 디버깅과정을 위해 디버거라는 툴이 따로 제공된다. 개발자는 디버거를 이용하여 정해진 과정을 따라 코드 속에 숨어있는 버그들을 제거해 나가면 된다.
하드웨어는 소프트웨어보다 디버깅이 까다롭다. 소프트웨어와 다르게 단계별 로그가 남아있는 것도 아니며 정형화된 디버거와 같은 툴이 있지 않다. 물론 딱 봐도 멋진 여러 정밀 측정장비가 있긴 하지만, 항상 그렇듯 눈에 멋져보이는 건 그림의 떡. 장비빨은 스타트업에겐 해당하지 않는다.
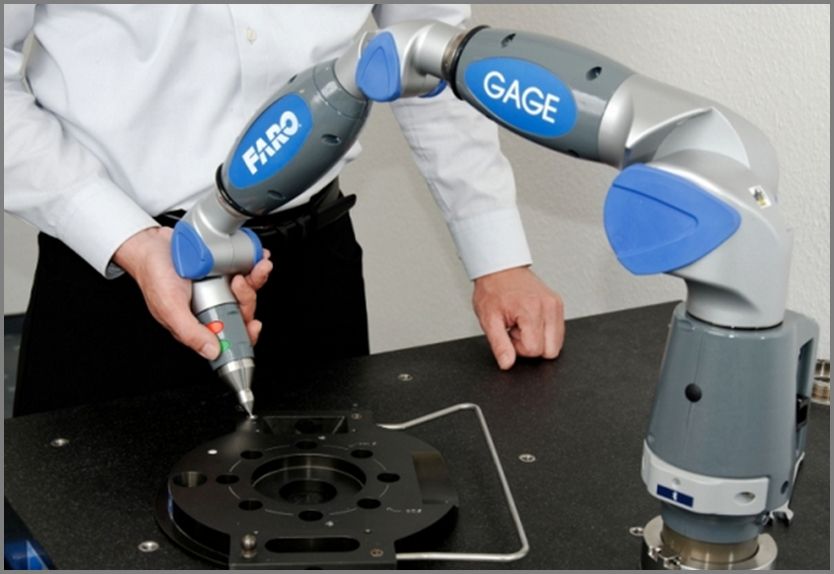
우리가 잘하고 지금도 하고 있는 방법은 직접 손으로 해보는 것이다. 제품 개발 간 문제가 생기면 더럽고 손에 잡아서 해볼 수 있는 것이라면 직접 손으로 만들어보면서 문제를 해결한 적이 꽤 많다.
물론 좋은 시뮬레이션이나 수십 년간 축적된 사람의 경험이 있으면 더욱 좋겠지만, 안타깝게도 우리는 없다. 그래서 우리는 우리가 할 수 있는 방법을 먼저 찾아서 빠르게 실행했다.
불 켜고 끄는 기계인 스위처가 잘 동작하는 제품이 되기 위해서 해결해야 하는 문제는 크게 아래 세 가지로 나눌 수 있었다.
- 스위치를 밀어주는 작동 장치가 필요하다.
- 사람이 수동으로 누를 수 있는 버튼이 필요하다.
- 내부 부품(회로기판,배터리)를 잘 내장해야 한다.
정말 운 좋게도(?) 모든 분야에서 문제가 터져 나왔다.
멋진 장비와 멋진 이론과 함께 검증하고 개발 해 나갈 수도 있지만, 스위처는 우리가 할 수 있는 것을 찾고, 가장 빠르고 확실한 방법을 택해서 문제를 해결 해 나갔다.
첫 번째 문제: 스위치를 밀어주는 작동 장치가 필요하다.
→ 기어의 크기를 0.00 단위로 다양화해서 직접 구동시켜보며 최적의 크기를 찾았다.
두 번째 문제: 사람이 수동으로 누를 수 있는 버튼이 필요하다.
→ 최적의 버튼감을 위해서 전면 버튼과 같은 재질의 넓은 판을 구하고, 다양한 사이즈로 컷팅하여 직접 손으로 눌러보며 테스트를 진행했다.
세 번째 문제: 내부 부품(회로기판,배터리)를 잘 내장해야 한다.
→ 수정이 매우 빠른 3D 프린터의 장점을 최대한 활용해 내부 부품 배치를 최적화해나갔다.
이렇게 하면 앞서 말한 1단계에서 3단계까지는 잘 작동하는 스위처를 만들 수 있었다. 우리는 준비가 끝났고 이제 공장에 가서 복사 붙여넣기만 할 일만 남은 줄 알았다.
[divide style=”2″]
‘금형’이라는 거대한 강을 만나다
그렇게 4단계, 금형이라는 넓은 강을 만나게 되었다. 강을 만났으니 나무를 자르고 엮은 다음 배를 만들어서 건너야 했다.
기껏해야 30개를 만들다가 1,700개를 생산해야 한다니. 게다가 아무 문제 없이 동작하고 고객에게 가치를 전달해야 하는 1,700개다.
금형? 대부분의 플라스틱 재질의 제품은 다량 생산을 위해 금형 공법을 이용하고, 금형을 이용해 플라스틱을 만들어 내는 과정은 붕어빵을 만드는 과정과 비슷하다.
이렇게 금형에서 제품을 찍어 내는 건 기존에 우리가 3단계까지 해왔던 방법과는 다른 점이 많다. 같은 이유에서인지 대부분 하드웨어 스타트업들이 이 단계를 수행하는데 적지 않은 시간을 투자하는 것으로 보인다.
스위처도 당연히 이 기간을 거쳤고 금형 제작(8월 12일)에서부터 제품이 나오는 데까지(9월 5일 사출 완료) 25일의 시간이 필요했다. 하지만 이제 소개할 금형을 위해 고민해야 하는 세 가지에 대해 미리 알았더라면 더욱더 빠르고 좋은 제품을 만들 수 있었을 것이다.
- 제품을 변형이 없게 생산할 궁리 = 살 빼기
- 금형 내에서 뻑뻑하게 굳은 제품을 빼낼 궁리 = 구배 주기
- 제품의 본래 형태를 그대로 유지하며 생산할 궁리 = 리브 주기
플라스틱은 온도에 민감하다. 따라서 플라스틱을 뜨겁게 녹이고 굳혀서 제품을 만드는 금형 공법의 특성상 제품에 변형이 올 수 있다.
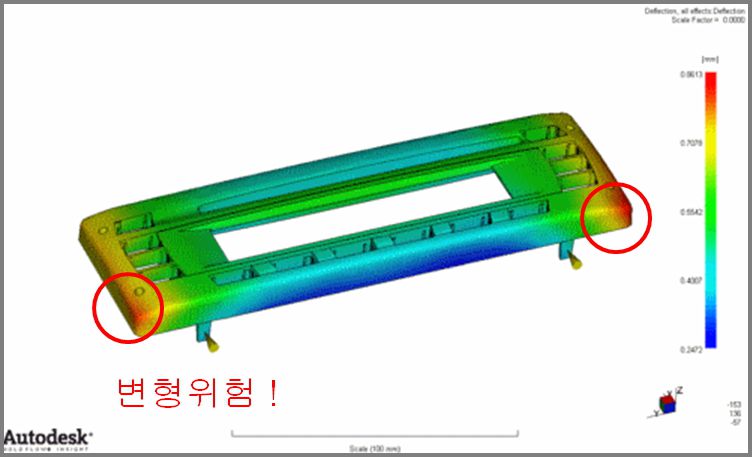
그중에 대표적인 변형이 수축현상이며 원인은 제품의 두껍고 일정하지 않은 두께가 주를 이룬다. 여러 가지 원인이 있지만, 두께가 원인이라면 제품을 다시 설계하는 수밖에 없으므로 치명적이다.
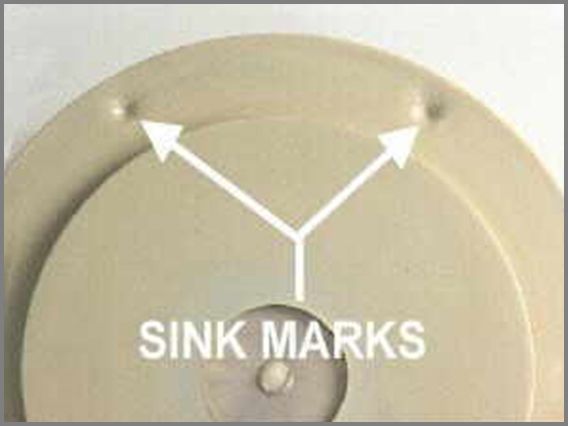
이를 방지하기 위해 제품의 두꺼운 부분에 임의적으로 구멍을 뚫는 살 빼기라는 작업을 통해서 제품의 두께를 최대한 똑같고 얇게 만들어서 수축현상을 방지한다.
아래 그림을 비교해보면 우측은 구멍이 뚫려있고 좌측은 구멍이 없다. 만약 제품을 아래 왼쪽 그림과 같이 설계해서 사출하면 노란색 원에서 수축이 일어날 것이다. 다른 부분에 비해 두께가 두껍기 때문이다.
다시 한 번 아래 사진을 살펴보면 수축이 의심 가는 부분이 또 있다. 어디에서 수축이 일어날 수 있을까?
노란색이 유력하다 판단할 수 있고 우측사진에서 보듯 실제로 수축이 일어났다. 엄청난 쪽팔림을 감수하고 여러분께 공개했으니 비웃진 말아달라.
따라서 기본적으로 좌측보다 우측이 좋은 설계라고 말한다. 두께가 얇을 뿐 아니라 일정하기 때문이다.
제품 초기 프로토타이핑 단계부터 일정한 두께를 고려해서 설계하면 제품 양산 시간을 줄이는 데 매우 많은 도움이 된다.
붕어빵틀에서 붕어 모양으로 퍼진 반죽이 맛있게 구워졌으면 이제 붕어빵을 떼어내야 한다. 그런데 만약 붕어빵이 붕어빵틀에 달라붙어서 붕어빵을 강제로 떼어 내다가 붕어빵이 터져버리면 그 붕어빵은 팔 수 없다.
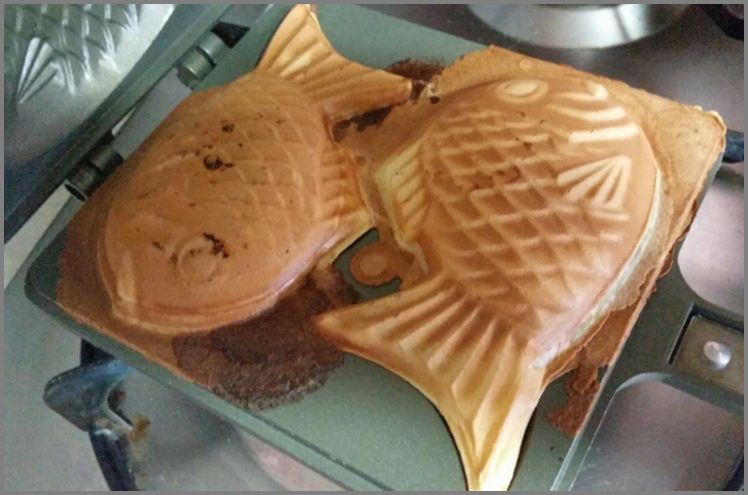
이와 똑같은 상황이 금형에서도 일어난다. 제품이 금형 안에서 굳고 나서 금형에서 제품을 떼어 내려고 하는데 제품이 잘 떨어지지 않아 필요 이상의 힘을 주어 빼내면 제품에 스크래치가 생겨 제품을 쓸 수 없다.
이를 방지하기 위해 설계 단계에서 제품을 매우 미세하게 기울인다. 다시 말해 제품 모양에 임의로 각도를 준다. 이것을 ‘구배’, 더 자세하게는 ‘빼기 구배’라고 한다. 금형에서 굳은 제품을 빼기 좋도록 구배를 준다는 의미이다.
스위처를 예로 들어보자.
구배는 스위처뿐만 아니라 플라스틱 사출로 만들어지는 제품에는 대부분 들어가 있다고 생각하면 된다. 이 말은 여러분들이 직사각형으로 생각했던 제품이 사실 정확히는 직사각형이 아니었음을 의미한다.
앞서 언급했듯,대부분 제품은 외벽이 얇게(1mm~2mm) 만들어지므로 하중을 버텨야 하거나 정확하게 사각형을 유지해야 하는 제품들의 경우 ‘휨’이라는 문제에 이를 수 있다. 스위처로 또 예를 들자면, 만약 위 제품을 사출한 제품을 쥐어 잡으면 흐물흐물한 오징어같이 본래의 형태를 유지하지 못하고 과도하게 휘게 될 것이다. 더더욱 스위처의 경우 내부에서 스위치를 미는 힘이 발생하기 때문에 제품이 휘게 되면 스위치를 밀 수 없다.
따라서 제품에 리브(rib)를 세운다. 단어 그대로 뼈대라고 생각하면 쉽다. 아래 사진처럼 내부에 갈비뼈를 촘촘히 세워주면 튼튼한 제품을 만들 수 있다. 스위처의 경우 리브가 강도 보강뿐 아니라 배터리 및 PCB(전자회로기판)의 받침대 역할까지 동시에 겸하고 있으며 이는 두께를 줄일 수 있는 핵심 요소다.
제품을 1개 만들 때와 1,700개를 만들 때는 이렇게 달랐다.
1,700개를 만들 때와 10,000개를 만들 때는 분명히 다를 것이다.
현재 스위처는 바로 그 단계에 와 있다.
10,000개라는 숫자에는 물건을 만드는 생산뿐 아니라 만든 물건을 잘 옮기고, 남는 물건을 잘 저장하는 고민까지 포함된 듯하다.
앞으로의 남은 과정에서도 스위처는 제품뿐만 아니라 서비스 전반적인 분야에서 앞선 과정과 같이 더럽지만 빠르게 검증하고 실행해서 기존 하드웨어 분야가 가지고 있던 속도라는 단점을 장점으로 끌어올리고 이를 통해 고객이 편리하고 쉽게 사용할 수 있는 제품을 만들 것이다.
잘 봤습니다. 자동차 금형 일을 했던 적이 있어 흥미깊게 봤네요.